Steam hoses are critical components in many industrial settings where the transfer of high-temperature steam or hot water is necessary. These hoses are employed in a variety of applications including cleaning processes, thawing, blow-out services, and fire prevention. Due to the high pressure and temperature of steam, steam hoses must be constructed to ensure reliability and safety, minimizing the risk of accidents and system failures. Steam hoses facilitate the efficient and safe transfer of steam, which is often used in demanding environments where precision and durability are essential.
Understanding Steam Hoses
Definition and Common Uses of Steam Hoses
Steam hoses are specially designed flexible hoses used to transfer high-temperature steam or hot water from one point to another in various industrial applications. They are typically employed in scenarios where steam or hot water is needed for processes such as:
Cleaning: Used in industries like food processing and manufacturing for cleaning equipment and surfaces.
Thawing: Applied in scenarios where frozen materials or machinery need to be thawed quickly.
Blow-Out Service: Utilized for blowing out debris and contaminants from equipment or pipelines.
Fire Prevention: Serves as a crucial component in fire suppression systems, where steam is used to control or extinguish fires.
These hoses are built to withstand high pressures and temperatures, making them essential for industries that rely on steam for critical operations.

Importance of Proper Construction for Safety and Efficiency
The construction of steam hoses is vital to their performance and safety. Proper construction ensures that the hose can handle the high pressures and temperatures associated with steam transfer. Key aspects of construction include:
Material Selection: The materials used in the hose construction must be able to resist extreme temperatures and the corrosive effects of steam. High-quality materials, such as EPDM rubber for the inner tube, contribute to the hose’s durability and performance.
Reinforcement: The reinforcement layer, typically made of braided or spiral steel wire, provides the strength needed to handle high-pressure steam. This layer prevents the hose from bursting under pressure and helps maintain its structural integrity.
Cover Protection: The outer cover protects the hose from external damage, such as abrasion, chemical exposure, and environmental factors. A well-designed cover extends the hose’s lifespan and ensures safe operation.
Key Components of Steam Hose Construction
Tube
Description of the Innermost Layer
The tube is the central layer of a steam hose, in direct contact with the steam or hot water. It is designed to withstand the high temperatures and pressures involved in steam transfer.
Materials Used (e.g., EPDM)
Typically made from high-quality synthetic rubber, such as EPDM (Ethylene Propylene Diene Monomer), the tube material is selected for its excellent resistance to heat and steam. EPDM is favored for its ability to handle temperatures up to 250°C (482°F) and its durability under prolonged exposure to steam.
Importance of Temperature and Chemical Resistance
The tube’s material must be resistant to thermal degradation and chemical reactions with the media it transports. Proper material choice ensures that the hose does not deteriorate quickly and maintains its performance over time.
Impact of Tube Diameter on Flow Capacity
The inner diameter of the tube directly influences the flow rate and capacity of the hose. A larger diameter allows for a higher volume of steam to pass through, whereas a smaller diameter may restrict flow and increase pressure.

Reinforcement Layer
The function of the Reinforcement Layer
The reinforcement layer surrounds the tube and provides structural support to the hose. Its primary functions include enhancing the hose’s ability to withstand internal pressures and preventing the hose from collapsing or kinking.
Types of Reinforcement (Braided vs. Spiral Steel Wire)
Braided Steel Wire: This type consists of interwoven steel wires that offer flexibility and resistance to high pressure. It is commonly used in hoses requiring flexibility and moderate pressure resistance.
Spiral Steel Wire: This reinforcement consists of steel wires arranged in a spiral pattern. It provides higher strength and pressure resistance, making it suitable for applications involving very high pressures.
Role in Handling High Pressures and Preventing Static Charges
The reinforcement layer is crucial for maintaining the hose’s integrity under high-pressure conditions and preventing the buildup of static charges, which could lead to electrical hazards or hose failure.
Cover
Description and Purpose of the Outer Layer
The cover is the external layer of the steam hose, designed to protect the internal components from environmental and mechanical damage. It acts as a shield against external factors that could impair the hose’s functionality.
Materials Used (EPDM, Chlorobutyl)
The cover is often made from EPDM or chlorobutyl rubber. EPDM offers good weather resistance and flexibility, while chlorobutyl provides superior resistance to chemicals and ozone.
Protection Against Corrosion, Weather, Chemicals, and Mechanical Abrasions
The cover is engineered to protect the hose from rust, UV rays, extreme weather conditions, and physical abrasions. This protection helps to extend the life of the hose and maintain safe operation.
Differences Between Oil-Resistant and Non-Oil-Resistant Covers
Oil-Resistant Covers: These are designed to withstand exposure to oils and fuels without degrading. They are essential for applications where the hose might come into contact with oily substances.
Non-Oil-Resistant Covers: These covers are suitable for environments where the hose is not exposed to oils. They are often used in cleaner environments to reduce costs without compromising performance.
Construction Standards and Specifications
Industry Standards for Steam Hose Construction
Steam hose construction is governed by various industry standards to ensure safety, reliability, and performance. Key standards include:
ISO 6134: This standard specifies the requirements for rubber and plastics hoses and hose assemblies for use with steam. It covers aspects such as material requirements, design specifications, and performance testing.
SAE J30: Though more commonly associated with automotive hoses, this standard also includes guidelines for hoses used in steam applications, focusing on their construction and performance under high-pressure conditions.
DIN 2828: A German standard for steam hoses, providing guidelines on the materials, design, and testing of hoses used in steam service.
ASTM D380: This standard covers the specifications for rubber hose and hose assemblies, including those used in steam applications, addressing aspects such as material properties and performance requirements.
Importance of Adherence to These Standards
Adhering to industry standards is crucial for several reasons:
Safety: Standards ensure that hoses are manufactured to withstand the pressures and temperatures they will encounter, reducing the risk of failures and accidents. Properly constructed hoses meet safety requirements that protect workers and equipment.
Performance: Compliance with standards guarantees that hoses will perform effectively in their intended applications. This includes maintaining flexibility, strength, and resistance to heat and chemicals, ensuring reliable operation.
Compatibility: Standards provide guidelines for compatibility with fittings and other system components. This helps in avoiding issues related to leaks, improper connections, and system failures.
Quality Assurance: Following established standards ensures consistent quality in hose manufacturing, leading to reliable and durable products that meet or exceed industry expectations.
How Specifications Affect Hose Performance and Safety
Material Specifications: The choice of materials based on standards affects the hose’s resistance to heat, pressure, and chemical exposure. For example, materials specified for high-temperature steam applications ensure that the hose will not degrade under extreme conditions.
Design Specifications: Standards dictate the design parameters, including wall thickness, reinforcement layers, and cover properties. These specifications impact the hose’s ability to handle high pressures, resist abrasion, and maintain flexibility.
Testing and Certification: Standards often include requirements for testing hoses to verify their performance and safety characteristics. Hoses that meet these testing criteria are certified for use in their specified applications, providing confidence in their reliability.
Operational Parameters: Specifications also define the operational limits of hoses, such as maximum temperature and pressure ratings. Adhering to these limits is essential for preventing hose failure and ensuring safe operation.
Installation Considerations
Proper Techniques for Installing Steam Hoses
Pre-Installation Inspection
Before installation, inspect the hose for any damage or defects. Ensure that the hose is compatible with the intended application, including checking its temperature and pressure ratings.
Correct Hose Routing
Route the hose to avoid sharp bends, kinks, or twists. Use proper supports and avoid placing the hose in locations where it could be subjected to mechanical damage or excessive abrasion.
Proper Fitting and Connection
Ensure that fittings and connections are properly matched to the hose specifications. Tighten fittings securely without over-tightening, which can damage the hose or fittings.
Use of Hose Supports
Employ appropriate supports to prevent the hose from bearing weight or being subjected to excessive movement. Supports should be placed to reduce stress and minimize potential damage.
Avoid Exceeding Bend Radius
Adhere to the hose’s minimum bend radius specifications to prevent kinking or collapsing, which can reduce the hose’s effectiveness and lifespan.
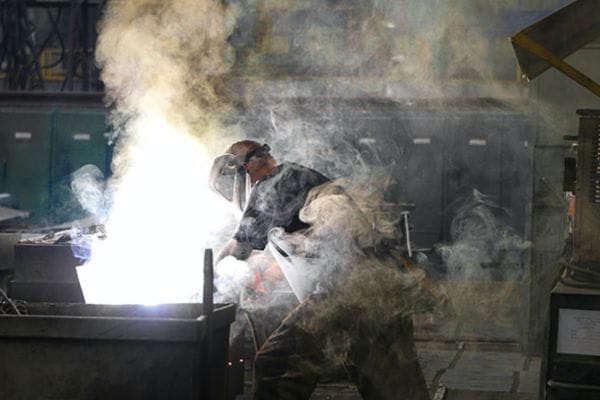
Common Mistakes to Avoid
Improper Hose Selection
Using a hose that does not meet the required temperature and pressure specifications can lead to premature failure. Always select a hose based on the specific demands of the application.
Incorrect Installation Techniques
Avoid installing hoses with sharp bends, kinks, or twists, as these can impair the flow and cause internal damage. Ensure hoses are not stretched or compressed during installation.
Neglecting Regular Maintenance
Failing to inspect and maintain hoses regularly can lead to unnoticed wear and tear, resulting in unexpected failures. Regular checks and maintenance are crucial for hose longevity.
Over-Tightening Fittings
Over-tightening fittings can damage both the hose and the fittings, leading to leaks or hose failure. Use the correct tools and follow manufacturer guidelines for tightening.
Ignoring Temperature and Pressure Ratings
Using hoses outside of their rated temperature and pressure limits can lead to dangerous failures. Always adhere to the specifications provided by the manufacturer.
Impact of Installation Practices on Hose Longevity
Reduced Wear and Tear
Proper installation practices, such as avoiding excessive bending and using appropriate supports, help minimize wear and tear on the hose, extending its operational life.
Prevention of Early Failures
Correct installation prevents issues like kinking, twisting, and mechanical damage, which can lead to early hose failures and costly repairs or replacements.
Enhanced Safety
Proper installation ensures that hoses operate within their designed parameters, reducing the risk of accidents and enhancing overall safety in the workplace.
Maintenance Efficiency
Properly installed hoses are easier to inspect and maintain, allowing for early detection of potential issues and more efficient maintenance practices.
Maintenance and Inspection
Regular Maintenance Practices for Steam Hoses
Routine Cleaning
Regularly clean the hose to remove contaminants that can cause damage or deterioration. After each use, drain and thoroughly dry the hose to prevent water buildup and potential ‘popcorning.’
Periodic Inspection Perform visual and physical inspections regularly. Check for signs of wear, damage, or deformation. Look for issues such as blisters, cracks, or exposed reinforcement.
Proper Storage
Store hoses in a manner that prevents damage. Avoid stacking heavy objects on them and ensure they are not bent beyond their minimum bend radius. Use hose racks or supports to maintain their shape.
Rust Protection
If a hose is not used for extended periods, apply rust protection to metal parts to prevent corrosion and potential leaks when the hose is put back into service.
Timely Replacement
Replace hoses that show significant signs of wear or have been in service beyond their recommended lifespan. Hoses typically need replacement after two years of use, even if they appear in good condition.
Signs of Wear and Potential Issues
Blisters and Lumps
Blisters or lumps on the hose cover can indicate internal damage or pressure issues. These can be caused by overheating or the accumulation of water vapor inside the hose.
Kinks and Twists
Kinks or twists in the hose can restrict flow and lead to increased wear or hose failure. Inspect for any permanent deformations and address them immediately.
Cracks and Tears
Cracks or tears in the hose cover can result from mechanical abrasion or exposure to harsh conditions. These defects can compromise the hose’s integrity and lead to leaks.
Exposed Reinforcement
An exposed reinforcement layer indicates that the hose cover has been damaged. This can lead to accelerated wear, rusting, and ultimately hose failure.
Leaks at Connections
Leaks at hose connections can signal issues with fittings or improper installation. Regularly check for leaks and ensure that fittings are securely fastened and in good condition.
Recommended Inspection Routines and Frequency
Pre-Use Checks
Inspect the hose before each use to ensure it is in good condition and free from visible damage. Look for issues such as cracks, blisters, and leaks.
Monthly Inspections
Conduct thorough inspections monthly to assess the overall condition of the hose. This includes checking for signs of wear, corrosion, and proper alignment.
Annual Review
Perform a comprehensive review of the hose system annually. This should include testing hose performance under operational conditions, verifying pressure ratings, and ensuring that all components are functioning correctly.
After Maintenance or Repair
Inspect the hose thoroughly after any maintenance or repair work to ensure that it has been reinstalled correctly and is functioning as intended.
Conclusion
By adhering to recommended practices and being aware of the key components and potential issues, you can significantly reduce the risk of hose failures, enhance operational safety, and prolong the service life of your hoses. Investing time in understanding steam hose construction is not just about compliance with industry standards but about safeguarding personnel and optimizing performance in critical applications.
FAQ
What is a steam hose?
A steam hose is a specialized hose designed to transport steam or hot water under high pressure and temperature, commonly used in cleaning, thawing, and fire prevention applications.
What materials are used in steam hoses?
Steam hoses typically consist of three layers: an inner tube made from EPDM rubber for temperature resistance, a reinforcement layer of braided or spiral steel wire for strength, and an outer cover for protection against external damage.
How do I know if my steam hose needs replacing?
Replace your steam hose if you notice visible damage such as cracks, blisters, or kinks, or if the hose has been in use for more than two years, even if it appears to be in good condition.
What are common signs of wear in a steam hose?
Common signs of wear include blisters on the cover, kinks or twists, exposed reinforcement, and leaks at the fittings.
How should I store steam hoses when not in use?
Store steam hoses properly by keeping them in a straight or slightly coiled position, avoiding heavy loads on top, and ensuring they are not bent beyond their minimum bend radius.
What maintenance is required for steam hoses?
Regular maintenance includes cleaning the hose after each use, inspecting it monthly for signs of wear or damage, storing it correctly, and applying rust protection to metal parts if stored for long periods.