O-rings are small but critical components in hydraulic systems, playing a crucial role in ensuring the overall system’s integrity by preventing leaks and maintaining pressure. These circular seals are often the difference between a smoothly operating hydraulic system and one plagued with costly downtime and fluid loss.
What Are O-Rings?
O-rings are doughnut-shaped seals typically made from elastomeric materials like rubber, silicone, or synthetic polymers. These rings are used as mechanical gaskets to create a tight seal between two or more parts, ensuring that fluids, gases, or air do not leak from the joints within hydraulic, pneumatic, or other types of systems. Despite their simple appearance, O-rings are a cornerstone of hydraulic applications, serving as the critical barrier that prevents fluid leakage, which can otherwise result in system inefficiencies, environmental hazards, and costly repairs.
In hydraulic systems, O-rings are most often positioned in grooves or cavities where two components join, such as fittings, valves, or flanges. When properly installed and compressed, the O-ring forms a seal that resists fluid flow through the gaps between these components, effectively maintaining pressure and preventing leaks. Their versatility, low cost, and ease of use make O-rings one of the most widely utilized seals in the industry, applicable in everything from simple machinery to advanced hydraulic systems in aerospace, automotive, and industrial applications.
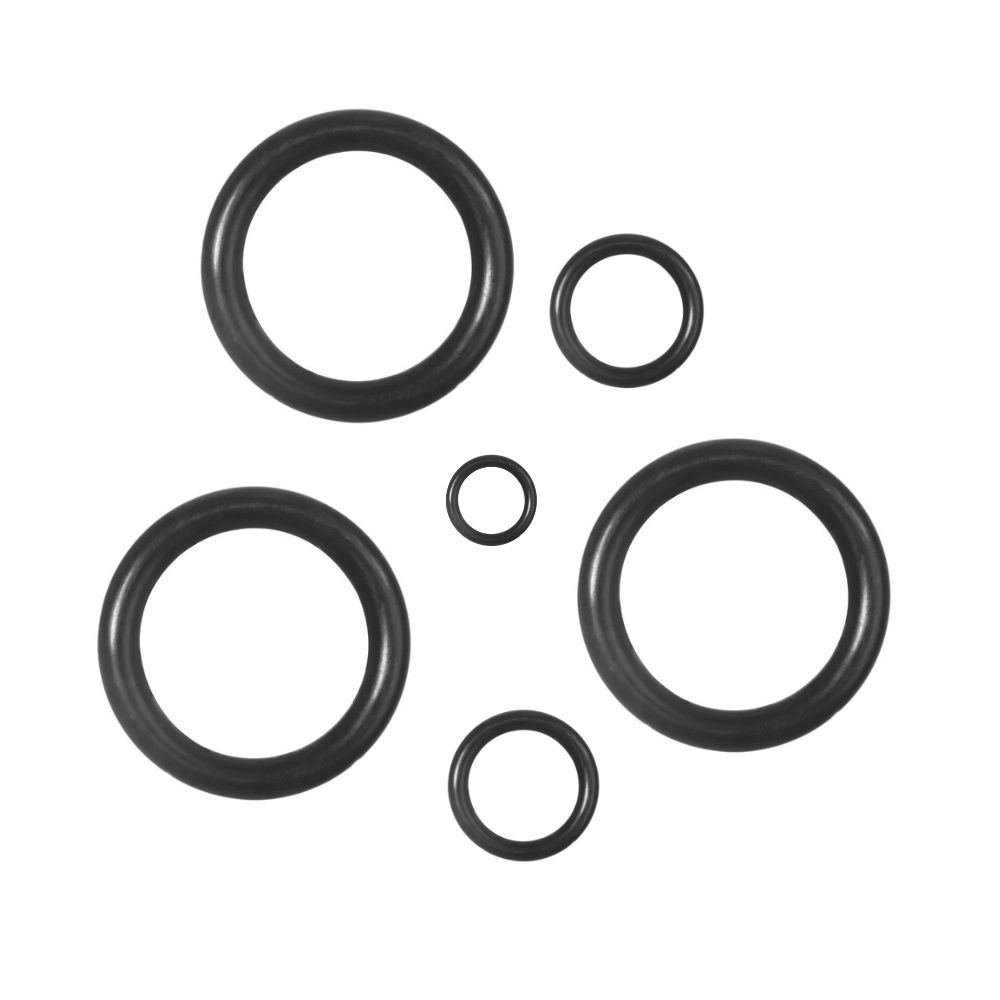
Types of O-Rings
O-rings come in various types, each designed for specific applications and system conditions. The two most common categories are static and dynamic O-rings:
Static O-rings: These O-rings are used in applications where the components being sealed do not move relative to one another. Static O-rings are often found in sealing joints, covers, or flanges, where the main function is to prevent leakage of fluid or gas in a stationary system. For example, in a hydraulic pump, static O-rings might be used to seal the housing to ensure the hydraulic fluid remains contained. Their simple design and limited exposure to friction mean they can last longer under appropriate conditions.
Dynamic O-rings: Dynamic O-rings, on the other hand, are used in applications where the sealed components move relative to each other. This could involve rotary motion (such as in rotating shafts or pistons) or reciprocating motion (such as in hydraulic cylinders). Dynamic O-rings face greater wear and tear due to continuous motion and are often subject to higher frictional forces. These O-rings must be made from more durable materials that can withstand mechanical stress, and lubrication is often critical to their long-term performance.
In addition to static and dynamic classifications, O-rings can also vary based on their material properties, which are selected to withstand specific environmental conditions like extreme temperatures, chemical exposure, or high pressures.
How O-Rings Function
The primary function of O-rings is to form a seal that blocks the flow of fluids or gases in a system. The sealing mechanism of an O-ring is based on its ability to deform and adapt to the space it occupies. When placed in a groove and compressed between two components, the O-ring material deforms, filling the small gap between the surfaces. This deformation creates a tight seal by ensuring that the fluid or gas cannot escape through any potential leak paths.
The effectiveness of this sealing mechanism relies on several factors:
Pressure: The amount of pressure applied to the O-ring during compression is critical to its performance. In hydraulic systems, the pressure of the fluid can push the O-ring further into the gap, enhancing the seal. However, excessive pressure can lead to O-ring extrusion, where the material is forced out of its groove, leading to failure. Therefore, the O-ring must be designed to handle the expected pressure range of the system.
Temperature: Temperature fluctuations can significantly affect O-ring performance. In hydraulic systems, where temperature may vary from extreme heat to freezing conditions, the material of the O-ring must be capable of maintaining its elasticity and shape. If the O-ring becomes too hard or brittle at low temperatures or too soft and pliable at high temperatures, it can fail to maintain a proper seal, leading to leaks.
Fluid Compatibility: O-rings must also be compatible with the hydraulic fluids they come into contact with. Different fluids can cause certain O-ring materials to swell, shrink, or degrade over time, compromising the seal. Selecting the correct material for the O-ring that can resist the specific chemicals and hydraulic fluids in the system is crucial to ensuring long-term performance and preventing premature failure.
The Importance of Material Selection in Hydraulic Applications
Impact of Incorrect Material Selection
Selecting the wrong material for O-rings in hydraulic applications can lead to a variety of issues that compromise the system’s overall performance and reliability. When the O-ring material is not suited to the environmental conditions or fluid it will encounter, premature failure is almost inevitable. This can manifest as cracking, swelling, hardening, or even complete disintegration of the O-ring. These failures not only result in fluid leakage but can also cause a cascade of other problems, such as pressure drops, contamination of hydraulic fluids, and even damage to other system components.
For example, using an O-ring material that is incompatible with the hydraulic fluid in a system can lead to chemical degradation. Incompatible materials may swell excessively or become brittle, reducing the O-ring’s ability to maintain a proper seal. This breakdown can cause leaks that, over time, may lead to costly repairs, fluid contamination, or even environmental damage due to leakage of hazardous fluids. Additionally, a malfunctioning seal can result in unplanned downtime, which can be expensive for industries where productivity is critical, such as manufacturing, construction, or mining.
Another impact of incorrect material selection is the potential for temperature-related failures. O-rings exposed to temperatures outside of their material’s tolerance range may harden or soften, losing their elasticity and sealing capabilities. In extreme cases, this can lead to a complete seal failure, which could trigger system malfunctions or even safety hazards. Thus, choosing the correct O-ring material is essential for maintaining the integrity of hydraulic systems and avoiding unnecessary failures and downtime.
Factors Affecting Material Choice
Fluid Compatibility:
One of the most critical factors in material selection is compatibility with the hydraulic fluid. Hydraulic systems often use a variety of fluids, including petroleum-based oils, synthetic fluids, water-glycol fluids, and even phosphate ester-based fluids. Each of these fluids can have a different chemical composition that may react negatively with certain O-ring materials. For instance, nitrile rubber (Buna-N) is well-suited for petroleum-based fluids but may degrade rapidly when exposed to phosphate ester fluids. On the other hand, Viton® (fluorocarbon rubber) offers excellent resistance to a wider range of chemicals, making it ideal for more aggressive fluid environments.

Temperature Extremes:
Hydraulic systems often operate in environments where temperatures can fluctuate significantly. High temperatures can cause some O-ring materials to soften or melt, while low temperatures can make them brittle and prone to cracking. Materials such as silicone rubber or Viton® are better suited for high-temperature applications, whereas nitrile and EPDM perform well in low-temperature conditions. Understanding the temperature range that the O-ring will be exposed to is crucial in selecting a material that will maintain its sealing properties under those conditions.
Pressure Requirements:
Hydraulic systems operate under varying pressure conditions, and the pressure levels exerted on O-rings can significantly impact their performance. In high-pressure systems, O-rings are subjected to extreme compressive forces, which can lead to extrusion—where the O-ring is forced out of its groove, compromising the seal. In such cases, materials with higher tensile strength and resistance to deformation, such as polyurethane or PTFE (Teflon®), may be necessary to handle the pressure. In lower-pressure systems, more flexible materials like nitrile may suffice. Choosing the correct material based on the system’s pressure requirements helps ensure that the O-ring will maintain a reliable seal without breaking down or extruding over time.
Overview of Common O-Ring Materials for Hydraulic Applications
Nitrile Rubber (Buna-N)
Properties:
Nitrile Rubber, also known as Buna-N, is one of the most commonly used materials for O-rings in hydraulic applications. It offers excellent resistance to petroleum-based fluids such as oils, fuels, and greases, making it a popular choice for many general-purpose hydraulic systems. Nitrile has good mechanical properties, including abrasion resistance, tensile strength, and flexibility. This makes it highly effective in moderate pressure environments and in applications requiring good sealing performance over a wide range of temperatures, typically from -40°C to 120°C.
Best Applications:
Nitrile O-rings are well-suited for hydraulic systems that use petroleum-based fluids and operate within moderate temperature ranges. They are commonly used in automotive, marine, and general industrial hydraulic systems. Nitrile’s durability and cost-effectiveness make it an ideal choice for applications where the operating environment is relatively stable and fluid compatibility is straightforward.
Limitations:
Despite its strengths, nitrile rubber has some limitations. It performs poorly when exposed to certain chemicals such as ketones, esters, and aldehydes, which can cause swelling or degradation. Additionally, at high temperatures, nitrile O-rings may lose their elasticity, leading to premature failure. It is also less effective in applications involving extreme temperatures, ozone exposure, or highly aggressive fluids.
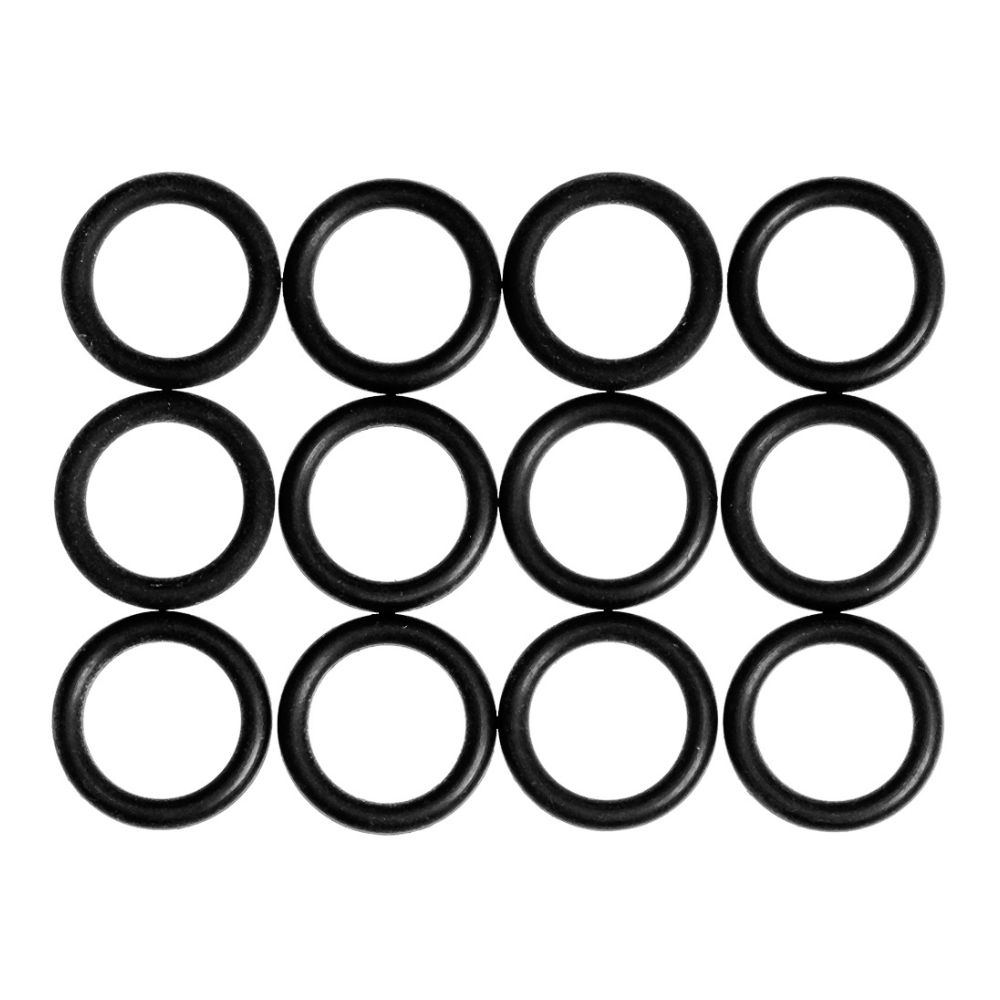
Viton® (Fluorocarbon)
Properties:
Viton®, a type of fluorocarbon rubber, is known for its outstanding heat resistance and chemical resistance, particularly to aggressive fluids like fuels, acids, and certain chemicals. It can withstand higher temperatures than many other O-ring materials, with a typical operating range of -20°C to 205°C, and can even endure short bursts of exposure to temperatures up to 315°C. Additionally, Viton® offers good resistance to ozone, weathering, and aging, making it ideal for long-term use in harsh environments.
Best Applications:
Viton® is particularly suitable for high-temperature hydraulic systems and environments where aggressive fluids are present. It is commonly used in aerospace, automotive, chemical processing, and industrial machinery where chemical exposure and elevated temperatures are concerns. Its ability to perform reliably in challenging conditions makes it an excellent choice for critical hydraulic applications.
Limitations:
One major limitation of Viton® is its higher cost compared to other O-ring materials like nitrile. Additionally, Viton® does not perform well at extremely low temperatures, as it can become brittle and lose its sealing properties. Therefore, it is not recommended for hydraulic systems operating in freezing environments.
EPDM (Ethylene Propylene Diene Monomer)
Properties:
EPDM rubber is known for its superior resistance to weathering, ozone, and certain chemicals, particularly in applications involving water-based fluids. It also offers good resistance to heat, steam, and some alkalis and acids. EPDM has a wide operating temperature range, from -45°C to 150°C, and performs well in outdoor environments where exposure to the elements is a concern.
Best Applications:
EPDM is ideal for hydraulic systems that use water-based fluids or are exposed to environmental factors such as ozone, UV light, and weathering. It is often used in systems involving brake fluids, water and steam applications, and outdoor equipment where environmental durability is important.
Limitations:
EPDM is incompatible with petroleum-based fluids, which can cause the material to swell and deteriorate rapidly. As a result, it is not suitable for most traditional hydraulic systems that rely on oil-based fluids. Additionally, while it is resistant to some chemicals, it does not perform well when exposed to oils, fuels, and hydrocarbons.
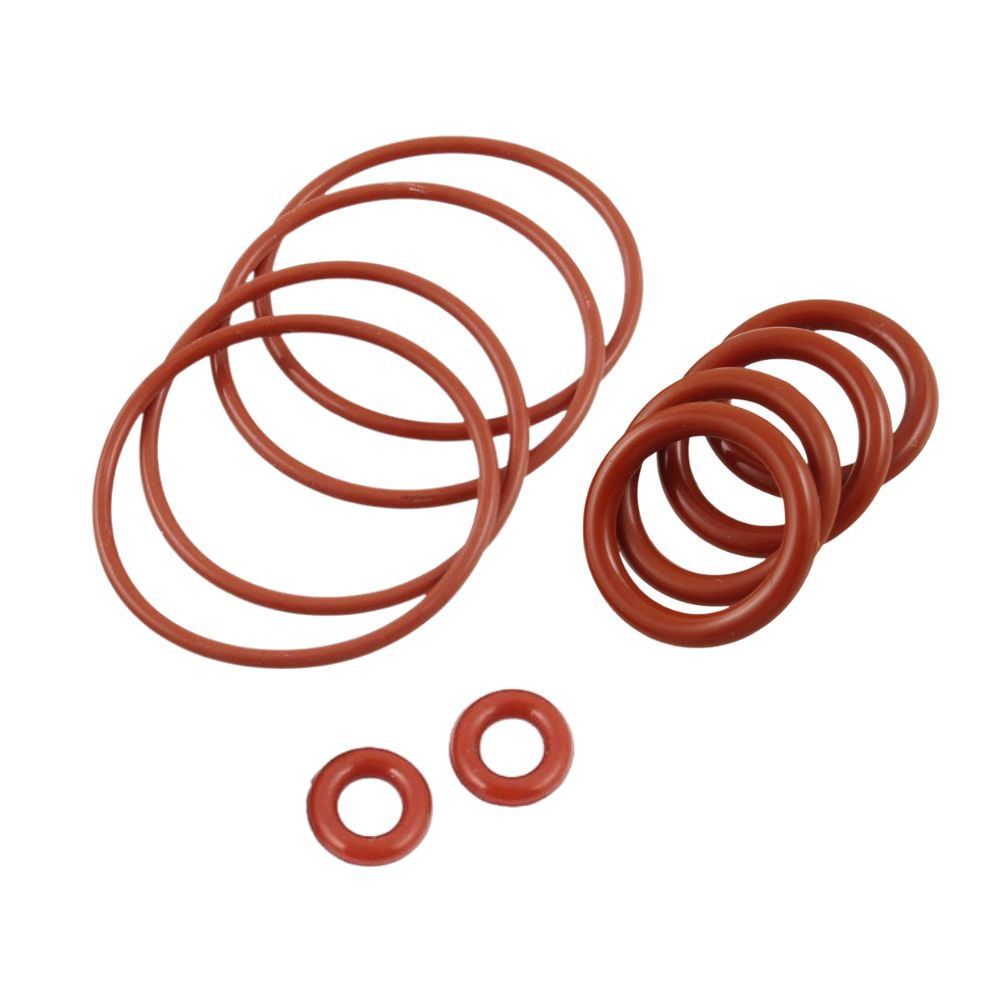
Silicone Rubber
Properties:
Silicone rubber is highly flexible and offers excellent heat resistance, with an operating temperature range of -55°C to 200°C. It is well known for maintaining its properties over a wide temperature range, making it suitable for both high and low-temperature applications. Silicone also has good electrical insulation properties and is highly resistant to UV light and ozone, contributing to its durability in outdoor environments.
Best Applications:
Silicone O-rings are commonly used in static applications where there is minimal motion between the sealed surfaces. These include aerospace, medical devices, and food processing equipment. Silicone performs well in environments with wide temperature variations, making it ideal for applications where both hot and cold conditions may be encountered.
Limitations:
While silicone offers excellent heat and environmental resistance, it has poor mechanical strength and is prone to tearing and abrasion, which limits its use in dynamic or high-pressure applications. Additionally, silicone is not resistant to petroleum-based fluids, making it unsuitable for most traditional hydraulic systems.
Neoprene
Properties:
Neoprene rubber offers a good balance of resistance to oils, greases, and weathering. It also has good mechanical properties, such as tensile strength and flexibility. Neoprene is resistant to moderate chemicals and can withstand exposure to environmental factors like ozone and UV light, making it durable in both indoor and outdoor settings.
Best Applications:
Neoprene is often used in applications where oil resistance is necessary, such as in refrigeration systems, automotive applications, and certain hydraulic systems. It is particularly effective in systems that require resistance to refrigerants and certain oils.
Limitations:
Neoprene has moderate resistance to heat and chemicals, and it may not perform as well in extreme temperatures or in contact with highly aggressive chemicals. Its operating temperature range is typically between -40°C to 120°C, making it less suitable for high-temperature applications.
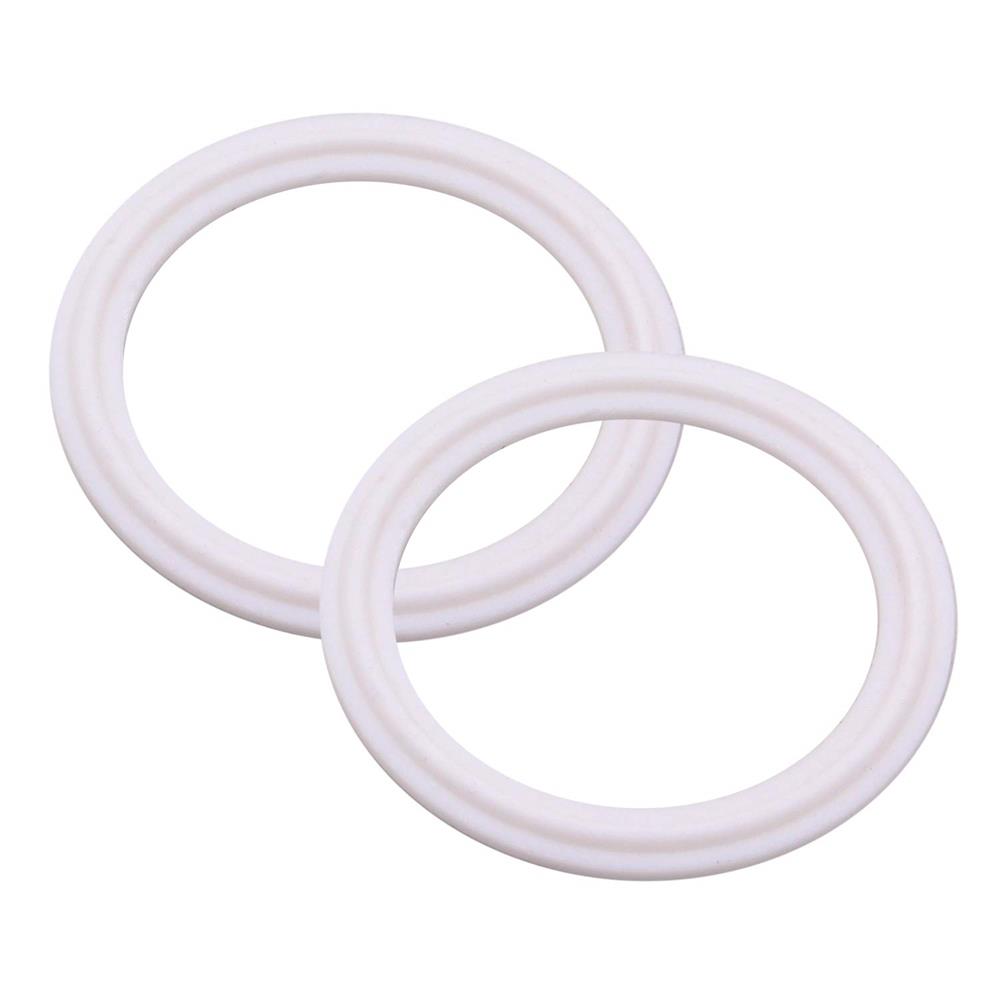
PTFE (Teflon®)
Properties:
PTFE, commonly known as Teflon®, is a highly durable material with exceptional chemical resistance and the ability to withstand extreme temperatures, ranging from -200°C to 260°C. PTFE is non-reactive to most chemicals and is highly resistant to corrosive substances, making it ideal for applications involving aggressive fluids. Its low friction coefficient also reduces wear and tear, enhancing its durability.
Best Applications:
PTFE O-rings are ideal for high-temperature hydraulic systems and applications involving aggressive fluids, such as in chemical processing, oil and gas, and pharmaceutical industries. They are also used in food processing equipment due to their inert properties and resistance to contamination.
Limitations:
PTFE O-rings can be more expensive than other materials, and their rigidity makes installation more difficult compared to elastomeric O-rings. Additionally, due to their lower elasticity, PTFE O-rings are less suitable for dynamic applications where significant movement or flexing is involved.
Key Factors in Material Selection for Hydraulic Applications
Fluid Compatibility
Explanation:
Fluid compatibility is one of the most critical factors in selecting the right O-ring material for hydraulic applications. The chemical composition of the hydraulic fluid determines how well the O-ring material will perform over time. If the O-ring material is not compatible with the fluid, it can degrade, swell, shrink, or harden, leading to leaks, seal failure, and system breakdown. Ensuring that the O-ring material is compatible with the specific hydraulic fluid is crucial for maintaining the integrity of the seal and the overall system.
Examples:
Petroleum-Based Fluids: Nitrile (Buna-N) is an excellent choice for systems using petroleum-based fluids such as hydraulic oils, fuels, and lubricants. Its resistance to these fluids makes it a common choice for general-purpose hydraulic systems.
Water-Glycol Fluids: EPDM is highly suitable for systems that use water-based hydraulic fluids like water-glycol mixtures. EPDM offers excellent resistance to water and steam, making it a great fit for these environments.
Phosphate Ester-Based Fluids: For hydraulic systems using phosphate ester-based fluids, Viton® (fluorocarbon rubber) is an ideal option. It provides excellent resistance to aggressive chemicals and high temperatures, ensuring that the O-ring can withstand harsh conditions.
Temperature Tolerance
Explanation:
The operating temperature of the hydraulic system plays a significant role in the performance and longevity of the O-ring. Extreme temperatures, whether high or low, can cause O-ring materials to harden, soften, or lose their elasticity, which can lead to failure and leaks. Proper material selection must consider the temperature range the system will be exposed to, ensuring that the O-ring can maintain its sealing properties throughout its service life.
High-Temperature Systems:
In high-temperature hydraulic systems, materials like Viton® (fluorocarbon rubber) perform exceptionally well. Viton® can withstand continuous exposure to temperatures up to 205°C, making it ideal for systems that operate under extreme heat, such as those found in aerospace or chemical processing industries.
Low-Temperature Systems:
For hydraulic systems operating in cold environments, materials like nitrile (Buna-N) are better suited. Nitrile maintains flexibility and sealing performance at low temperatures, with an effective operating range down to -40°C. This makes it a good choice for applications where freezing temperatures may be encountered, such as in cold storage or outdoor equipment.
Pressure Requirements
Explanation:
Pressure is another key factor influencing O-ring selection. Hydraulic systems often operate under high pressures, which place significant stress on the O-rings. The higher the pressure, the greater the likelihood that the O-ring will be compressed or extruded out of its groove. Selecting an O-ring material that can withstand the specific pressure conditions of the system is critical to ensuring the longevity and reliability of the seal.
High-Pressure Systems:
In high-pressure environments, O-rings made from materials with strong compression set resistance, such as PTFE (Teflon®) or polyurethane, are ideal. These materials are less prone to deformation and extrusion, ensuring that the seal remains intact even under extreme pressures. PTFE, in particular, is highly resistant to compression and is used in applications where maintaining the seal at high pressures is crucial.
Low-Pressure Systems:
For systems operating at lower pressures, more flexible materials like nitrile or silicone can be used. These materials offer sufficient sealing performance without the need for the more rigid, compression-resistant properties required in high-pressure applications. This makes them cost-effective choices for systems where pressure demands are less intense.
Wear and Tear
Explanation:
In dynamic hydraulic applications where components are in constant motion, O-rings are subject to wear and tear from friction, mechanical stress, and continuous use. Durability and mechanical resistance are essential qualities for O-ring materials used in such systems. Without the proper level of abrasion resistance, O-rings can wear out quickly, leading to frequent maintenance, replacement, and potential system failure.
Materials with High Abrasion Resistance:
Nitrile (Buna-N) is one of the most commonly used materials in dynamic applications due to its excellent abrasion resistance. It is well-suited for systems with frequent motion and mechanical stress, such as hydraulic cylinders and pumps. Other materials like polyurethane, which also offers high tensile strength and resistance to mechanical wear, are often used in demanding applications like construction or mining equipment, where frequent motion and heavy loads are common.
Conclusion
Now is the perfect time to assess your hydraulic system and determine if the O-ring materials you are using are truly suited to your application’s needs. Evaluate the operating conditions, fluid types, and pressure ranges in your system, and ensure that your O-ring selection aligns with these variables. Proper material selection will not only enhance the performance of your system but also extend the life of your components, reducing maintenance costs and avoiding unplanned downtime.
FAQ
What is the primary function of an O-ring in a hydraulic system?
O-rings act as a seal to prevent fluid leaks and maintain pressure within the hydraulic system by filling the gap between two components.
How do I choose the right O-ring material for my hydraulic system?
Select the material based on fluid compatibility, temperature range, pressure requirements, and the level of mechanical stress the O-ring will encounter.
Can I use the same O-ring material for all types of hydraulic fluids?
No, different fluids require specific O-ring materials. For example, nitrile is suitable for petroleum-based fluids, while EPDM works better with water-based fluids.
What happens if I use the wrong O-ring material in my hydraulic system?
Using the wrong material can lead to premature failure, leaks, system downtime, and potential damage to other components due to degradation or chemical incompatibility.
How often should I replace O-rings in my hydraulic system?
Regular inspection is essential, and O-rings should be replaced if there are signs of wear, cracking, or hardening, or if they no longer maintain a proper seal.
What is the maximum temperature O-rings can withstand?
The maximum temperature depends on the material. For instance, Viton® can handle temperatures up to 205°C, while nitrile is limited to around 120°C.