Hydraulic fittings are vital components in fluid systems, designed to connect, secure, and direct the flow of hydraulic fluids between machinery parts. They come in various shapes, sizes, and materials, depending on the application, and play a critical role in ensuring system efficiency and safety. Properly selected fittings maintain pressure, prevent leaks, and enable smooth connections between components like hoses, pipes, and valves.
Step 1: Familiarize Yourself with Different Hydraulic Fitting Types
Understanding the various types of hydraulic fittings is the first step in identifying the right ones for your system. Hydraulic fittings come in different shapes, sizes, materials, and connection methods, and each type is designed for specific applications. In this section, we’ll break down the most common types of hydraulic fittings you’ll encounter and their key features.
Overview of Common Hydraulic Fitting Types
There are several categories of hydraulic fittings, and each serves a unique purpose in fluid systems. The most common types include:
- Threaded Fittings – These fittings have threaded ends that screw into corresponding components, creating a tight seal. They are commonly used in stationary applications and where high pressure is involved.
- Flared Fittings – These are designed with a flared end that fits into a corresponding connector, usually involving a metal-to-metal seal. They are ideal for high-pressure systems.
- Compression Fittings – Often used for smaller systems, compression fittings use a ferrule to compress the tube against the fitting, creating a secure, leak-proof connection.
- Push-to-Connect Fittings – These fittings are designed for quick and easy connection without the need for tools. They are ideal for applications where flexibility and speed are required.
- Quick Connect Fittings – Similar to push-to-connect, these allow for the fast connection and disconnection of hydraulic hoses or equipment without needing extra tools or hardware.
Knowing how to identify these different types is essential for correctly selecting the right fitting for your hydraulic system.
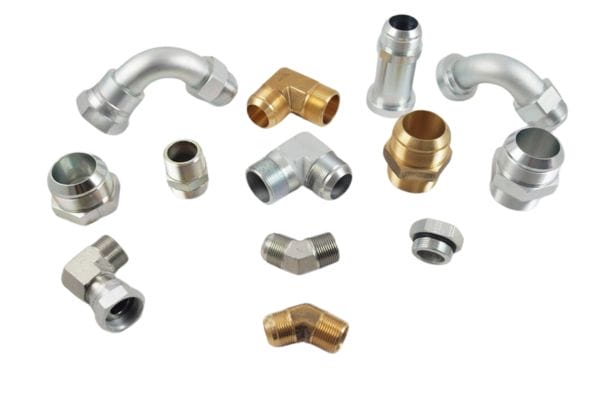
Threaded Fittings: NPT, BSPT, BSPP
Threaded fittings are among the most common hydraulic fitting types, and they feature threads that allow them to screw into compatible components. Here are the three most common types of threaded fittings:
- NPT (National Pipe Thread): This is a tapered thread type commonly used in North America. It creates a seal by the threads themselves, which tighten as they are screwed into place. NPT fittings are often used in high-pressure applications but require careful installation to avoid leaks.
- BSPT (British StandardPipe Tapered): Similar to NPT, BSPT fittings have a tapered thread and are primarily used in Europe and parts of Asia. The tapered threads create a tight seal, but these fittings should not be confused with BSPP (explained below), as they are designed for different types of systems.
- BSPP (British StandardPipe Parallel): Unlike BSPT, BSPP fittings have parallel threads and require a seal, such as an O-ring or gasket, to prevent leaks. These are commonly used in low-pressure systems and where a flexible seal is needed.
Key Differences to Remember:
NPT has tapered threads, while BSPT has similar but slightly different thread angles and shapes.
BSPP uses parallel threads and relies on seals for a leak-proof connection.
NPT and BSPT are used in high-pressure systems, while BSPP is used for low-pressure systems.
Flared Fittings vs. Compression Fittings
When working with hydraulic systems, it’s crucial to understand the differences between flared and compression fittings, as they are designed for different types of connections.
- Flared Fittings: These fittings are used with tubing that has been flared at the end, creating a wide, cone-like shape that fits tightly against the fitting’s tapered surface. Flared fittings create a strong metal-to-metal seal, which makes them ideal for high-pressure applications where tight sealing is critical. They are commonly used in gas and fluid systems where leak prevention is a top priority.
- Compression Fittings: Compression fittings use a ferrule to compress the tubing against the fitting, creating a secure, leak-free connection. These fittings are generally used in low to medium-pressure applications and are popular in smaller hydraulic systems. They are easier to install than flared fittings but may not handle high-pressure conditions as well.
Key Differences to Remember:
Flared fittings require tubing to be flared at the end and are best for high-pressure systems.
Compression fittings use a ferrule to secure the tube and are best for low-pressure and smaller applications.
Push-to-Connect and Quick Connect Fittings
These two fitting types are designed for ease of use and fast connection and disconnection, making them particularly useful in dynamic or mobile hydraulic systems.
- Push-to-Connect Fittings: These fittings allow quick installation by simply pushing the tube or hose into the fitting. The fitting automatically locks into place, creating a tight, secure connection without requiring any tools. Push-to-connect fittings are ideal for systems where fast, frequent connections are needed, and they are often used in automation and pneumatic systems.
- Quick Connect Fittings: Quick connect fittings are designed for rapid connection and disconnection of hydraulic hoses and equipment. Unlike push-to-connect, quick connect fittings often feature a lever or collar that, when activated, locks or unlocks the connection. These fittings are commonly used in systems where components are regularly swapped in and out, such as construction or agricultural machinery.
Key Differences to Remember:
Push-to-connect fittings are easy to install without tools and are used in low-pressure applications.
Quick connect fittings allow for rapid connection and disconnection, making them ideal for equipment that needs to be frequently connected and disconnected.
Step 2: Learn How to Identify Hydraulic Fitting Sizes
When it comes to hydraulic fittings, selecting the right size is crucial for ensuring that fluid flows efficiently and without leakage. Hydraulic fittings come in various sizes, and understanding the difference between nominal size and actual size, as well as how to measure and determine the correct size, is key to proper system functionality.
Understanding Nominal Size vs. Actual Size
Nominal Size refers to the approximate internal diameter of the fitting or hose, which is often used as a standard measurement. It is a rough indication of the size and is often rounded for convenience. Nominal sizes are typically denoted in inches or millimeters, but they do not always correspond exactly to the actual dimensions of the fitting.
Actual Size refers to the true measurements of the fitting, including its outer diameter (OD) and inner diameter (ID), and can vary slightly from the nominal size. Understanding this distinction is important, as hydraulic systems require precise measurements to ensure that fittings and hoses fit securely and provide a leak-free connection.
For example:
A “1/2-inch” hydraulic fitting might have a nominal size of 1/2 inch, but its actual inner diameter could be slightly different due to manufacturing tolerances.
When choosing hydraulic fittings, it is essential to check both the nominal and actual sizes to ensure compatibility with your system’s hoses and pipes.
Measuring Hydraulic Fitting Diameter and Length
Correctly measuring the diameter and length of hydraulic fittings is key to making sure you select the right components for your system. Here’s how to do it:
- Measuring the Diameter: To measure the diameter of a hydraulic fitting, use a caliper to determine the outside diameter (OD) or inner diameter (ID) of the fitting. For threaded fittings, measuring the diameter at the base of the threads is important. If you’re working with hoses, the inside diameter is especially critical, as it affects the fluid flow.
- Measuring the Length: The length of the fitting typically refers to the overall length, from one end of the fitting to the other. For threaded fittings, this includes the length of the threads. It’s important to measure the entire length of the fitting, including any parts that will be inserted into the connecting components (such as the threaded or flared section).
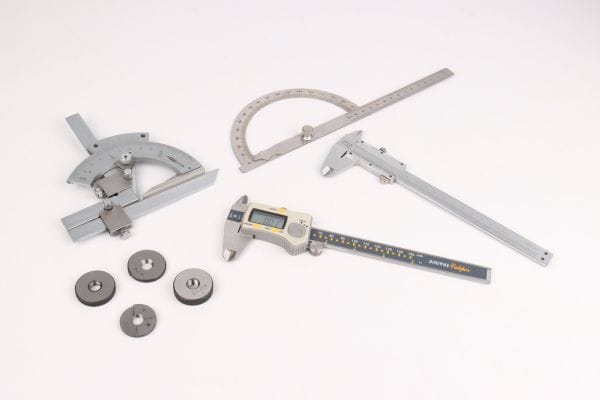
How to Determine the Correct Size for Your System
Selecting the correct hydraulic fitting size requires a careful approach. Here are the steps to ensure you choose the right fitting size for your system:
- Check Hose or Tube Size: The size of the hose or tube that you are using is the primary determinant for selecting the fitting size. Measure the inner diameter (ID) of the hose or tube and ensure it matches the fitting size.
- Match the Fitting Type to the Application: Different types of fittings are designed to accommodate specific applications, so ensure that the fitting size matches the required flow rate and pressure. For instance, high-pressure systems may require fittings with thicker walls or larger sizes.
- Consult Manufacturer Specifications: Manufacturers often provide charts or guidelines for selecting the correct fitting size based on the hydraulic system’s pressure requirements and fluid types. These charts help you match the fitting size to your system’s needs.
- Consider the Thread Type and Size: If you are using threaded fittings, be sure to match the thread type (NPT, BSPT, BSPP, etc.) with the correct size. Threads should match both the diameter and pitch to ensure a secure connection.
- Account for System Pressure and Flow Requirements: The size of the fitting also depends on the pressure and flow rate of your hydraulic system. Larger fittings are required for systems with higher flow rates, while smaller fittings may suffice for low-pressure systems.
Step 3: Understand Hydraulic Fitting Materials
Selecting the right material for hydraulic fittings is critical for ensuring that your system operates reliably under varying pressures, temperatures, and environmental conditions. Different materials offer distinct advantages in terms of strength, corrosion resistance, durability, and cost. Understanding these materials will help you make informed decisions to optimize your hydraulic system’s performance.
Material Properties and Their Impact on Performance
The choice of material significantly influences the overall performance of hydraulic fittings in your system. Key properties of each material type impact how the fittings will function under different conditions:
Strength and Durability
- Steel fittings provide the highest strength and are often used in heavy-duty applications, such as in mining, construction, or manufacturing, where high-pressure conditions are common.
- Brass fittings, being softer, are not as strong and are more suited to light-duty applications, such as in fluid handling or low-pressure systems.
- Stainless steel fittings strike a balance between strength and corrosion resistance, and are ideal for systems exposed to aggressive chemicals, high temperatures, or harsh environments.
Corrosion Resistance
- Steel fittings are vulnerable to corrosion if not properly coated or treated, particularly in environments with moisture or exposure to chemicals.
- Brass fittings are more resistant to corrosion than carbon steel, but they can still degrade under certain conditions, particularly in high-temperature or high-pressure environments.
- Stainless steel fittings offer the best corrosion resistance, making them the ideal choice for offshore applications, marine environments, and systems exposed to harsh chemicals.
Temperature Tolerance
- Steel fittings can tolerate a wide range of temperatures, but they may rust or weaken in extreme moisture or corrosive conditions unless treated.
- Brass is less tolerant of high temperatures compared to steel or stainless steel and is typically used for lower-temperature systems.
- Stainless steel excels in both high and low temperatures and maintains its integrity in extreme conditions, making it the preferred choice for applications with temperature variations.
Choosing the Right Material for Your Hydraulic System
When selecting the material for your hydraulic fittings, consider the following factors to ensure optimal performance:
- System Pressure and Flow Rate: If your system operates at very high pressures, steel fittings may be the best option due to their superior strength. For moderate pressure systems, brass or stainless steel may be more appropriate.
- Environmental Conditions: If your hydraulic system will be exposed to harsh chemicals, moisture, or extreme temperatures, stainless steel fittings are ideal due to their corrosion resistance and durability. For systems in less aggressive environments, brass may be a suitable choice.
- Corrosion Resistance Needs: For applications exposed to water, salty environments, or chemicals, stainless steel fittings provide superior corrosion resistance. Brass also offers some resistance but may not be as durable as stainless steel in these conditions.
Step 4: Get to Grips with Hydraulic Fitting Threads
Hydraulic fittings rely heavily on precise thread types to ensure secure connections and prevent leaks. Understanding the different thread types used in hydraulic systems and knowing how to identify and match them correctly is essential for system efficiency and safety.
How to Identify Thread Types in Hydraulic Fittings
Identifying the correct thread type in hydraulic fittings is crucial, as each thread type has a specific design and function. Here’s how you can identify them:
- Inspect the Threads: The first step in identifying thread types is to visually inspect the threads on the fitting. Check for characteristics like whether the threads are tapered or parallel, as this can immediately narrow down your options.
- Measure the Thread Pitch: Thread pitch refers to the distance between adjacent threads. To measure it, use a thread pitch gauge or calipers. The pitch can be measured in inches (for imperial threads) or millimeters (for metric threads).
- Identify the Thread Form: The thread form (the shape of the thread profile) is another key indicator. Some common forms include triangular (for NPT threads), square (for BSPP threads), or rounded forms (for JIC threads).
- Use a Thread Identification Chart: Once you’ve identified basic features like pitch and form, use a thread identification chart to confirm the thread type. Charts will show the exact measurements and form for popular hydraulic thread types.
Tips for Matching Threads Correctly
Incorrectly matched threads can lead to leaks, system inefficiency, or even catastrophic failure. Here are some practical tips for ensuring you choose the right threads:
Match the Thread Type and Size
Make sure the fitting and the connecting component (pipe or hose) have the same thread type and size. This is critical to achieving a proper, leak-proof seal. Always double-check whether the fitting requires tapered threads (like NPT or BSPT) or parallel threads (like BSPP or metric threads).
Use a Thread Pitch Gauge
A thread pitch gauge is a useful tool for identifying the thread pitch and determining whether the pitch of the fitting matches the corresponding hose or pipe. A slight mismatch in pitch can cause an incomplete seal, leading to leaks.
Check for Sealing Mechanisms
For tapered threads (NPT, BSPT), the threads themselves create the seal as the fitting is tightened. For parallel threads (BSPP, JIC), sealing relies on an additional element like an O-ring or copper washer. Ensure that the sealing component is also the correct size and material for the application.
Pay Attention to Thread Angle
Thread angle plays a vital role in ensuring a secure connection. For example, NPT has a 60-degree angle, while BSPT has a 55-degree angle. If the wrong type of thread is matched (e.g., BSPT with NPT), the threads may not engage correctly, causing leaks or failure.
Verify System Pressure Requirements
Consider the pressure rating of the system when choosing fittings. Some threads, like NPT, are designed to handle high-pressure environments, while others, like BSPP, may be more suited for low-pressure systems with O-ring seals. Ensure that the fitting thread type can handle the pressure your system requires.
Consider Thread Coatings
Thread coatings (such as PTFE or nickel plating) can help improve the performance of the thread, especially in systems exposed to chemicals or high temperatures. If the system is highly corrosive, choosing fittings with appropriate coatings can help extend the life of the threads and prevent wear or corrosion.
Step 5: Examine Hydraulic Fitting Connections and Seals
Hydraulic fitting connections and seals are crucial elements in maintaining the integrity of your hydraulic system. A proper connection ensures that pressure is maintained, fluid flows seamlessly, and leaks are prevented. Understanding the different types of connections and seals, as well as how to identify the right ones for your system, is essential for ensuring reliability and safety in hydraulic operations.
Types of Hydraulic Fitting Connections: Male, Female, Couplings
Hydraulic fittings come with different types of connections that allow them to securely attach to hoses, pipes, and other components in the hydraulic system. Here’s an overview of the most common types:
Male and Female Connections
- Male Fittings: Male hydraulic fittings have external threads that fit into female counterparts. These fittings are typically used to connect to a female fitting or port. Male fittings are commonly used in straight-thread and tapered-thread applications.
- Applications: Connecting hoses to a valve, pump, or cylinder port. Common in systems using NPT or BSPT threads.
- Female Fittings: Female hydraulic fittings have internal threads that allow them to connect with male fittings. They are commonly used in threaded port connections where a male fitting is inserted into the female connector.
- Applications: Used in hydraulic systems to connect tubes or pipes to components like pumps, cylinders, and valves.
Couplings
- Quick-Connect Couplings: These are designed to provide quick and easy connections between hydraulic lines without the need for tools. They allow users to disconnect or connect hydraulic lines with minimal effort, which is especially useful in mobile or field applications.
- Applications: Agricultural machinery, construction equipment, or systems requiring frequent changes between hoses or tools.
- Threaded Couplings: Threaded couplings are used to connect two components with matching threads. They provide a more permanent and secure connection and are common in industrial hydraulic systems.
- Applications: Used where a secure, leak-proof connection is necessary, typically in industrial or high-pressure applications.
- Flanged and Clamp Couplings: Flanged couplings use a flange and bolts to connect pipes or hoses, providing a strong, secure connection. Clamp couplings use a clamping mechanism for easy assembly and disassembly. Both are typically used in larger hydraulic systems.
Applications: High-flow systems, heavy equipment, and large-scale industrial machinery.
Identifying Proper Seals for Hydraulic Fittings
Identifying the correct seal for your hydraulic fittings is just as important as selecting the right fitting itself. Here are some key factors to consider when choosing seals:
Material of the Seal
The material of the seal directly affects its performance in the hydraulic system. The most common seal materials include:
- Nitrile (Buna-N): This is a common seal material, used in general-purpose hydraulic systems. It is resistant to petroleum-based fluids but has limitations at higher temperatures.
- Viton (FKM): Known for excellent resistance to high temperatures and a broad range of chemicals, Viton seals are ideal for systems with high-temperature or aggressive fluid environments.
- EPDM (Ethylene Propylene Diene Monomer): EPDM seals are highly resistant to water and steam and are commonly used in applications where water or glycol-based fluids are present.
- PTFE (Polytetrafluoroethylene): PTFE seals are known for their low friction and excellent chemical resistance, making them suitable for systems that deal with aggressive chemicals or high-pressure environments.
Seal Shape and Type
There are several different types of seals used in hydraulic fittings, each designed for specific applications:
- O-rings: One of the most commonly used seals in hydraulic fittings, O-rings are circular seals that fit into grooves and provide a reliable, pressure-tight connection. They are used in various fitting types, including flared fittings and threaded connections.
- Backup Rings: These rings are used in conjunction with O-rings to prevent extrusion in high-pressure environments. They support O-rings in situations where extreme pressure could cause the O-ring to deform.
- Face Seals: Face seals provide a sealing surface between two parts and are commonly used in high-pressure hydraulic systems. They provide a leak-tight connection without the need for an additional sealing element like an O-ring.
- Gaskets: Gaskets are often used in flanged hydraulic connections to provide a seal between two flat surfaces. They are designed to compress when tightened to ensure a leak-free connection.
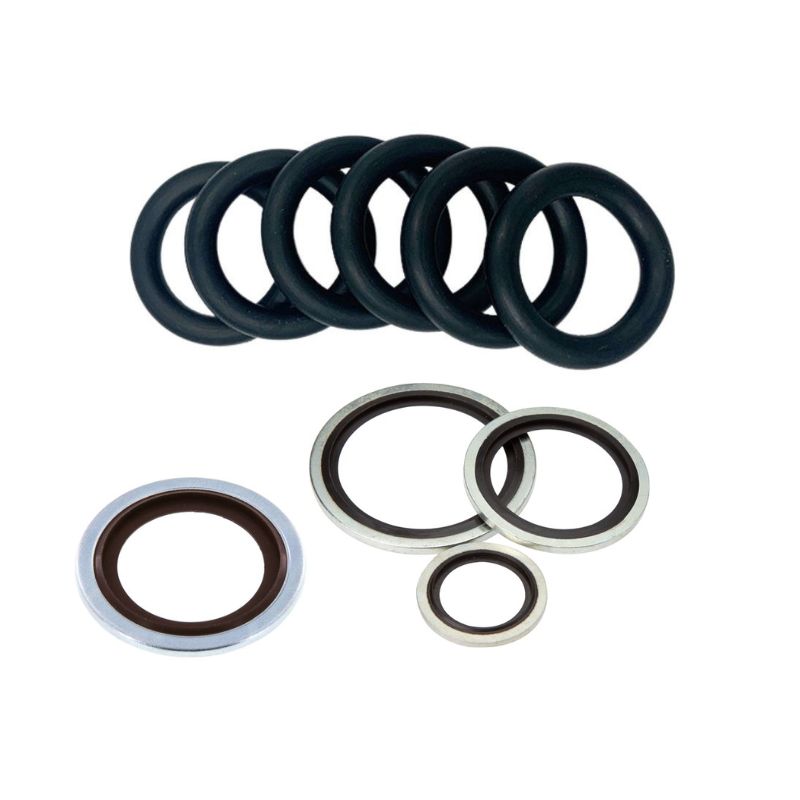
Pressure and Temperature Rating
The seal’s material and design must be able to withstand the operating pressure and temperature of the hydraulic system. Check the manufacturer’s specifications for pressure and temperature limits to ensure the seal is appropriate for your system’s demands.
Fluid Compatibility
Ensure that the seal material is compatible with the hydraulic fluid used in your system. Hydraulic fluids vary widely in terms of chemical composition, and some materials (e.g., nitrile) may degrade if exposed to certain fluids. Always verify compatibility before choosing a seal material.
Seal Sizing
Ensure the seal is the correct size for the fitting and the application. A seal that is too large or too small may not provide a proper seal, leading to leaks. Always refer to manufacturer specifications for seal dimensions and sizing.
Step 6: Check Hydraulic Fitting Pressure Ratings
The pressure rating of hydraulic fittings is a critical factor in ensuring the safety and reliability of your hydraulic system. Hydraulic systems operate under varying levels of pressure, and using fittings with incorrect pressure ratings can lead to catastrophic failures, leaks, or damage to the system.
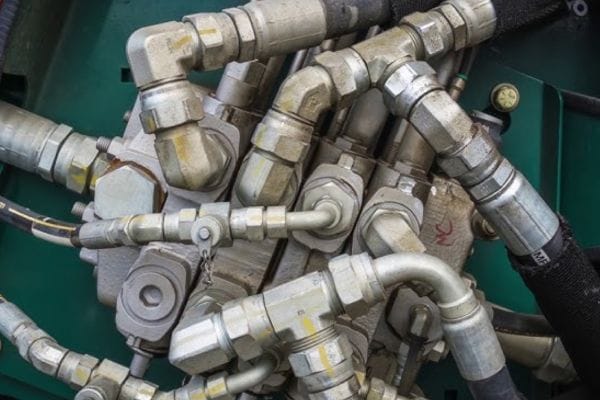
Common Pressure Rating Standards for Hydraulic Fittings
Hydraulic fittings come with specific pressure ratings that are determined by factors like the material of the fitting, the design, and the intended use of the system. Here are some common standards for pressure ratings:
PSI (Pounds per Square Inch)
PSI is the most commonly used unit to express pressure in hydraulic systems, especially in the United States. Hydraulic fittings are rated to withstand pressures measured in PSI. The pressure ratings of fittings are often marked directly on the fitting itself or provided in the manufacturer’s specifications.
- Low-Pressure Fittings: These typically have pressure ratings up to 1,500 PSI and are used in systems where low pressures are involved, such as in lubrication systems or cooling applications.
- Medium-Pressure Fittings: Rated around 3,000 to 5,000 PSI, these fittings are commonly found in industrial hydraulic systems for machinery and equipment.
- High-Pressure Fittings: These fittings are designed to withstand pressures above 5,000 PSI and are often used in heavy-duty applications such as construction machinery, aerospace, and hydraulic presses.
MPa (Megapascal)
In countries that use the metric system (like Europe), pressure ratings may be expressed in megapascals (MPa). One MPa is equal to 145 PSI, and hydraulic fittings in these regions may be rated for 10 MPa, 25 MPa, or higher, depending on the application.
Bar
A bar is another metric unit of pressure used widely in Europe. One bar is approximately equal to the pressure exerted by a 1 kg weight per square centimeter at sea level. Hydraulic fittings may be rated in bars, with common ratings being 100 bar (low-pressure systems), 400 bar (medium-pressure systems), and 700 bar or more (high-pressure systems).
SAE Standards (Society of Automotive Engineers)
SAE J514 and SAE J516 standards are commonly used for hydraulic fittings in North America. These standards provide pressure ratings based on the material and fitting design. For example, SAE J514 specifies the pressure ratings for flareless fittings made from steel, which can typically handle pressures up to 5,000 PSI.
ISO Standards (International Organization for Standardization)
ISO 8434 is a set of standards used for hydraulic fittings, particularly in Europe and international markets. These standards define pressure ratings based on the design, material, and intended application. Common ISO pressure ratings include those for fittings used in automotive, industrial, and mobile machinery.
Identifying the Right Pressure Rating for Your System
Choosing the right pressure rating for hydraulic fittings depends on various factors, including the operating conditions, fluid type, and system design. Here are key steps for identifying the correct pressure rating for your system:
Know Your System’s Maximum Operating Pressure
The first step in selecting a hydraulic fitting with the correct pressure rating is to know the maximum operating pressure (MOP) of your system. This is the highest pressure your system will experience under normal operating conditions. Always choose a fitting with a pressure rating higher than your system’s MOP to ensure safety.
Factor in Pressure Surges
Hydraulic systems can experience pressure surges or spikes that exceed the normal operating pressure. To account for these surges, select fittings with pressure ratings that can handle transient pressures. Typically, you should choose a fitting rated at least 1.5 times the system’s normal operating pressure to accommodate these spikes.
Temperature Considerations
Pressure ratings can also be influenced by temperature. High temperatures can weaken materials, while extremely low temperatures can make certain materials brittle. If your system operates in extreme temperatures, consider how temperature affects the fitting’s pressure rating and select fittings designed for those conditions.
Factor in Fluid Type
Certain fluids (such as water-based fluids, oil, or synthetic fluids) may have different effects on hydraulic fittings. Fluids with higher viscosity or corrosive properties may require fittings with higher pressure ratings. Ensure the hydraulic fluid in your system is compatible with the fitting material and its pressure rating.
Step 7: Ensure Compatibility with Your Hydraulic System
Ensuring compatibility between hydraulic fittings and your system’s components is essential to achieving peak performance, avoiding system failures, and maintaining safety. When hydraulic fittings are mismatched with the system’s requirements, it can lead to poor fluid flow, leaks, and even complete breakdowns.
Matching Fittings to the Hydraulic System’s Requirements
Choosing the right fittings for your hydraulic system starts with understanding the specific needs of your system. Each hydraulic system is unique, with varying pressure, flow, and temperature demands, so selecting the appropriate fittings requires careful consideration.
Consider the System’s Application and Design
Each hydraulic system has a specific purpose, whether it’s for heavy machinery, industrial manufacturing, or mobile equipment. Understanding the intended application of your system helps determine which fittings are necessary to ensure smooth operation. For example:
- Heavy-duty machinery: Will require high-pressure-rated fittings and robust materials like steel or stainless steel.
- Mobile equipment or machinery: Might benefit from quick-connect fittings for ease of maintenance and flexibility.
Choose Fittings Based on System Pressure
Different sections of a hydraulic system will have different pressure requirements. It’s essential to choose fittings that can handle both the maximum operating pressure (MOP) and any potential pressure surges or spikes. Ensure that all components, including hoses, fittings, and valves, are rated for the pressures they will experience in service.
Select Fittings for Fluid Compatibility
Hydraulic systems use different types of fluids such as water-based fluids, petroleum-based oils, or synthetic fluids. The material of the fittings must be compatible with the fluid used in your system to prevent corrosion, leakage, or damage to components. Always verify the fluid compatibility of both the fitting material and seals, as some materials may degrade when exposed to certain fluids.
Account for Environmental Conditions
The operating environment of your hydraulic system plays a significant role in the type of fittings you select. Exposure to harsh elements such as extreme temperatures, chemicals, UV radiation, or corrosive conditions may require fittings made from specialized materials (e.g., stainless steel, brass, or corrosion-resistant coatings) that can withstand such environments.
Understanding Flow Rate and Compatibility
Flow rate refers to the volume of hydraulic fluid that moves through the system per unit of time, typically measured in gallons per minute (GPM) or liters per minute (LPM). Ensuring compatibility between the flow rate and the hydraulic fittings is essential to maintaining efficient system operation.
Matching Flow Rate with Fitting Size
Fittings must be sized to allow for proper flow through the system. Choosing fittings that are too small can restrict fluid flow, increase pressure drop, and cause system inefficiency. On the other hand, oversized fittings can lead to turbulence and fluid instability, which can cause wear and tear on system components. To match the flow rate with the fitting size:
Ensure the internal diameter (ID) of the fitting matches the diameter of the hose or pipe to avoid flow restriction.
Use fittings with the appropriate flow characteristics to maintain system pressure and prevent unnecessary fluid resistance.
Pressure Loss Considerations
Pressure loss due to friction is a key factor when selecting fittings, especially when considering the flow rate. If the fittings are too small for the flow rate, the system will experience a pressure drop, which could affect the operation of downstream components like pumps and valves. To minimize pressure loss:
Use fittings designed to reduce friction, such as those with smooth internal surfaces.
Select fittings that are designed for low-flow or high-flow applications, depending on the system’s needs.
Flow Control Components Compatibility
In some systems, flow control components such as valves, pumps, and regulators are used to manage the flow of fluid. Ensure that the fittings selected are compatible with these components to maintain the required flow rates and pressure settings. For example, if your system uses a flow control valve, make sure the fittings match the specifications of the valve and the hoses connected to it.
Conclusion
In conclusion, mastering the art of recognizing hydraulic fittings is a vital skill for anyone working with hydraulic systems. If you still have questions about how to properly identify hydraulic fittings, feel free to contact us!
FAQ
What are hydraulic fittings, and why are they important?
Hydraulic fittings are components used to connect hoses, pipes, or tubes in hydraulic systems. They ensure the safe and efficient transfer of hydraulic fluid between system components. Properly chosen hydraulic fittings prevent leaks, maintain pressure, and ensure the system operates smoothly.
How do I determine the correct size of a hydraulic fitting?
To determine the correct size, you need to measure both the internal diameter (ID) and the external diameter (OD) of the hose or pipe that the fitting will connect to. Make sure to consider both the nominal and actual size of the fitting to ensure a proper fit and prevent leaks.
What materials are used in hydraulic fittings?
Common materials for hydraulic fittings include steel, brass, stainless steel, and carbon steel. The material selection depends on the type of fluid used, environmental conditions, pressure ratings, and compatibility with other system components.
How can I identify the thread type of a hydraulic fitting?
Hydraulic fittings often have different thread types, such as NPT (National Pipe Thread), BSPT (British Standard Pipe Tapered), and BSPP (British Standard Parallel). To identify the thread type, check the fitting’s thread pitch, size, and whether it is tapered or parallel. Use a thread gauge or comparison to confirm the correct match.
What’s the importance of hydraulic fitting pressure ratings?
Pressure ratings indicate the maximum pressure that a hydraulic fitting can safely handle. It is crucial to choose fittings with a pressure rating that matches or exceeds the maximum pressure your hydraulic system will experience. Using a fitting with an inadequate pressure rating can result in system failure, leaks, or damage.
How do I ensure compatibility between hydraulic fittings and my system?
To ensure compatibility, consider the system’s pressure, fluid type, flow rate, and environmental conditions. Match the fitting material, size, thread type, and pressure rating to the system’s requirements.